Data Capture Solutions for Logistics Management
High-performance data capture providing reliable barcode reading throughout the mobile delivery process
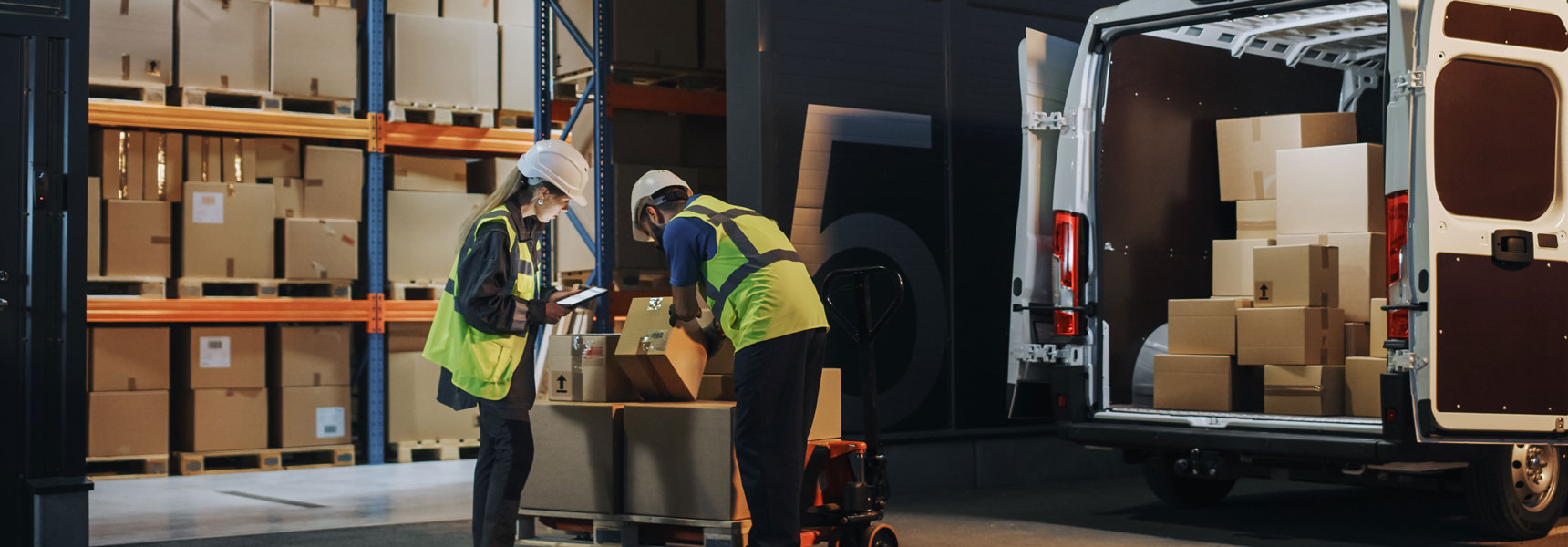
Transportation solutions for logistics
Distribution workers are the ones who fulfill a product's promise by physically delivering products to customers. Tracking and handling merchandise in transit can be a difficult and time-consuming task. Miscalculations on deliveries and stocking are easy to make, which is why a secure and dependable tracking system needs to be in place, ensuring deadlines are met and orders are fulfilled.
With data capture and delivery solutions, Socket Mobile’s barcode scanners and RFID readers aid logistics systems by providing real-time reflections of orders in transit, enabling a constant connection to corporate networks. Coordinating the details of a business's deliveries and stocking can be laborious, back-breaking, and headache-inducing. Socket Mobile’s scanning solutions reduce that stress just a little bit.
Logistics Solutions
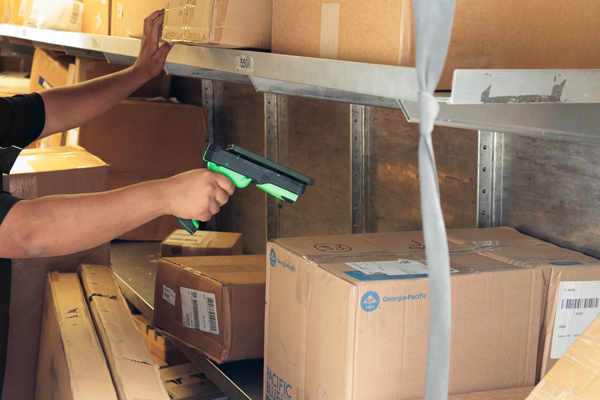
Benefits of integrating into your logistics management system
Choosing Socket Mobile means more than just choosing a simple data collection tool. We provide long-lasting benefits and support that will ultimately give you complete confidence in choosing us for your logistics management system.
-
SocketCam, our free camera-based barcode scanner, is included in CaptureSDK. SocketCam lets you start scanning or testing your app immediately without needing a physical scanner. Using the camera in the user’s mobile phone or tablet, CaptureSDK with SocketCam provides commercial-grade barcode scanning solutions. With one integration, you and your users get access to high-performance camera-based scanning along with our full portfolio of data readers, allowing seamless interchange or upgrades without requiring app revisions.
-
With one integration of CaptureSDK users have access to our entire line of barcode scanners and readers. As scanning volume grows and users need enhanced performance, upgrading their solution is easy and painless.
-
Our barcode scanners help eliminate common human errors, such as those made when inputting data into your system manually. We provide instant, reliable data collection so you can feel confident with all data collected.
-
Socket Mobile goes beyond just helping you choose the best scanner for your business environment. We provide full support throughout the setup process to meet your needs throughout the entire data collection journey.
-
Socket Mobile's data readers provide real-time updates and accurate tracking of goods at every stage of the supply chain. This visibility minimizes human errors, ensures timely deliveries, and streamlines the overall order fulfillment process, making it easier to manage complex logistics networks.
-
Socket Mobile devices are the most reliable option when you need scanners and readers to work for hours while reading personal information. Our scanners and readers have exceptionally low breakage and return rates, giving you the utmost confidence that your data collection device will always be ready to go.
-
All Socket Mobile data readers are cordless. With all-day rechargeable batteries, you can work safely and efficiently throughout your environment.
Recommended products
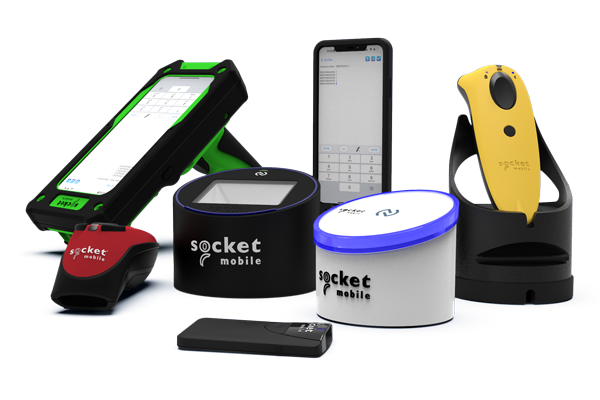
Case studies
A courier company needed a quick and reliable solution for scanning packages in real-time and verifying whether the postage was paid. Socket Mobile provided the solution, and delivery staff are now able to scan and verify customers' packages on the go.
A martial arts fighting gear provider implemented a Socket Mobile barcode scanner into everyday delivery operations for package tracking, scanning barcodes on locations, boxes, inventory, incoming stock, and returns.
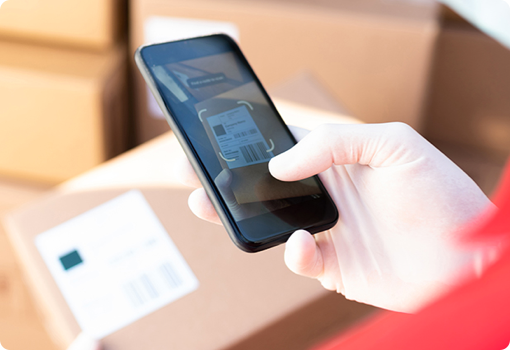